熱可塑性CFRP(炭素繊維強化プラスチック)を用いた研究開発について
1.概要
世界的な自動車への環境規制を背景として、自動車の軽量化を目指した研究開発が世界で進行しています。軽量化において有望視されている材料としてCFRP※1があり、これまでは熱硬化性※2CFRPが利用されていましたが、力学的特性に優れるものの成形性・融着性に課題があり、航空機や一部の高級車への適用に留まっていました。
これら課題の解決に向けて、NEDO事業※3において、ISMAの組合員である名古屋大学の石川隆司(いしかわ たかし)特任教授らのチームは、成形性・融着性に優れる熱可塑性※4CFRPに着目し、かつ、LFT-D(Long Fiber Thermoplastics.Direct)工法を用いた開発に取り組んできました。その結果、自動車のシャシー部材の成形をこれまでより圧倒的に速く、1分程度で完了させ、また、超音波融着法※5を用いたシャシー組み立て技術によって、熱可塑性CFRPのみによる自動車用シャシーの製作に世界で初めて成功しました。 今回、材料供給から最終製品までの一貫自動生産が可能になり、部材コストの低減にめどを立てることができました。これにより、CFRPの量産自動車への適用の加速が期待されます。
今後、自動車の車体軽量化や部材の量産化が加速されることにより、自動車によるCO2排出量の削減が見込まれ、世界の環境問題の解決に貢献することが期待されます。
2.今回の成果
LFT-D工法(ドイツのフラウンホーファー研究機構で最初に着想された繊維強化プラスチックの製造方法、図1参照)は、連続的に炭素繊維を供給して熱可塑性樹脂ペレットと混練し、比較的長い炭素繊維長を保って混練機から押し出される素材を高圧プレスに供給、短時間に所望の構造部材を成形する方法です。オートクレーブ法※6では必要となる中間工程が今回の方法では不要となるため、熱可塑性樹脂と炭素繊維の供給から最終製品までの一貫自動生産システム構築が可能となり、短時間成形を実現しました。
また、熱可塑性CFRPの融着可能な利点を生かしてシャシー部材を接合することで、オール熱可塑性CFRP製シャシーの製作に成功しました。
今回、ロボットを活用した超音波融着システムを構築したことで、複雑な実構造体の高速接合が可能になりました。
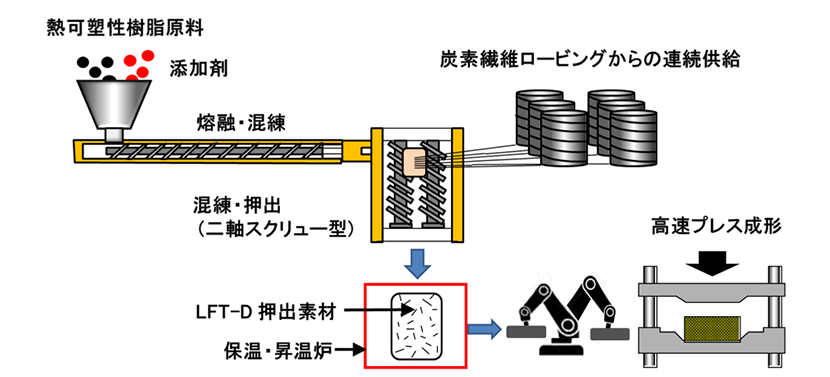
LFT-D工法の概念図
3.今後の展望
NCCでは、今後、LFT-D工法で製作される部材の力学的特性向上に注力するとともに、成形時の反りを抑制した高精度成形技術の確立を目指します。また、超音波融着技術においては、鉄鋼材料の接合で用いられるスポット溶接と等価レベルの高速接合技術を開発していきます。
NEDOは、本成果と合わせ、他の構造材料の開発を推進するとともに、これら異種材料を統合するマルチマテリアル化技術に取り組み、輸送機器の抜本的軽量化を目指します。
※1 CFRP:Carbon Fiber Reinforced Thermoplasticsの略。炭素繊維強化プラスチック。炭素繊維と樹脂を複合した軽量・高強度な材料。連続繊維強化型と非連続繊維強化型がある。
※2 熱硬化性:プラスチックの中で、温度を上げていくと硬化するものの持つ性質。対立する性質として、熱可塑性がある。
※3 NEDO事業:事業名/革新的新構造材料等研究開発、事業期間/2014年度〜2022年度、事業内容/鉄鋼、非鉄(チタン、アルミニウム、マグネシウム)、CFRPといった構造材料の特性を向上させ、自動車を中心とした輸送機器の軽量化を図る事業。ナショナルコンポジットセンターは熱可塑性CFRP材料の開発を担当している。
※4 熱可塑性:プラスチックの中で、温度を上げていくと柔らかくなって融解するものの持つ性質。対立する性質として、熱硬化性がある。
※5 超音波融着法:熱可塑性樹脂等を超音波振動と加圧力によって溶融させ、部材同士を接合する技術。
※6 オートクレーブ法:複合材部品の加熱・加圧成形をオートクレーブ(圧力釜)で行う方法で、主に航空機の構造部材成形で用いられる。
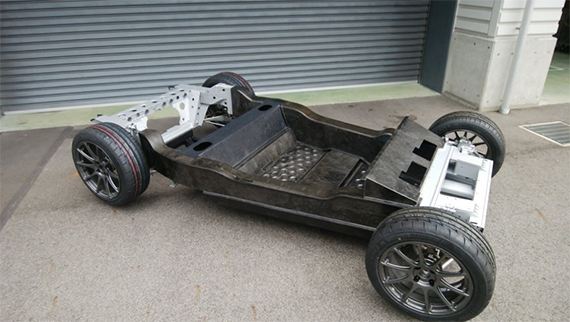
完成した熱可塑性CFRPシャシーにタイヤを付けて展示用としたもの
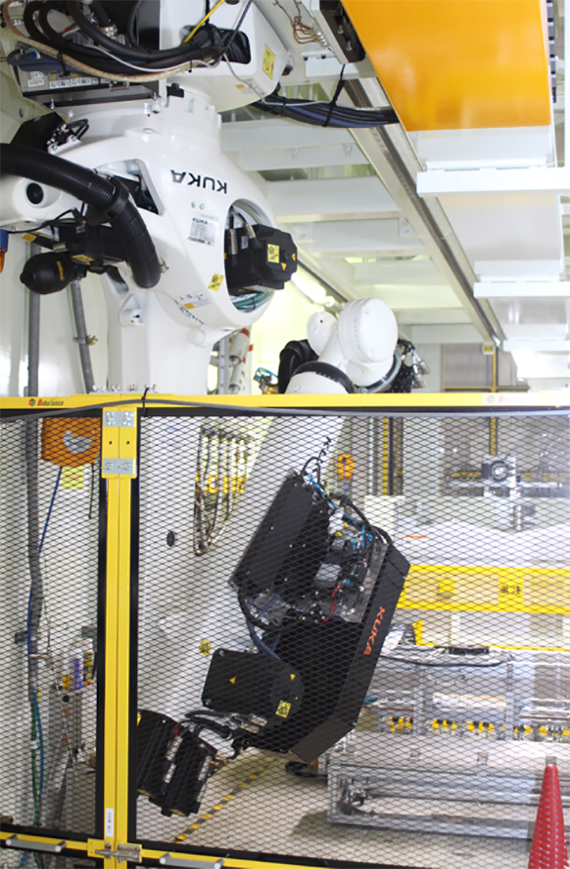
シャシーの一部であるサイドシルなどの部品の製造に使用されるロボット